Tungsten, molybdenum, and rhenium are critical refractory materials in the semiconductor industry due to their exceptional thermal stability, high melting points, and excellent electrical conductivity. These materials are widely used in semiconductor manufacturing for applications such as diffusion barriers, gate electrodes, and interconnects in integrated circuits. Their ability to withstand extreme temperatures and corrosive environments ensures reliable performance in advanced processes like chemical vapor deposition (CVD) and physical vapor deposition (PVD). By enabling miniaturization and enhancing device performance, these refractory materials play a vital role in driving innovation and progress in the semiconductor industry.
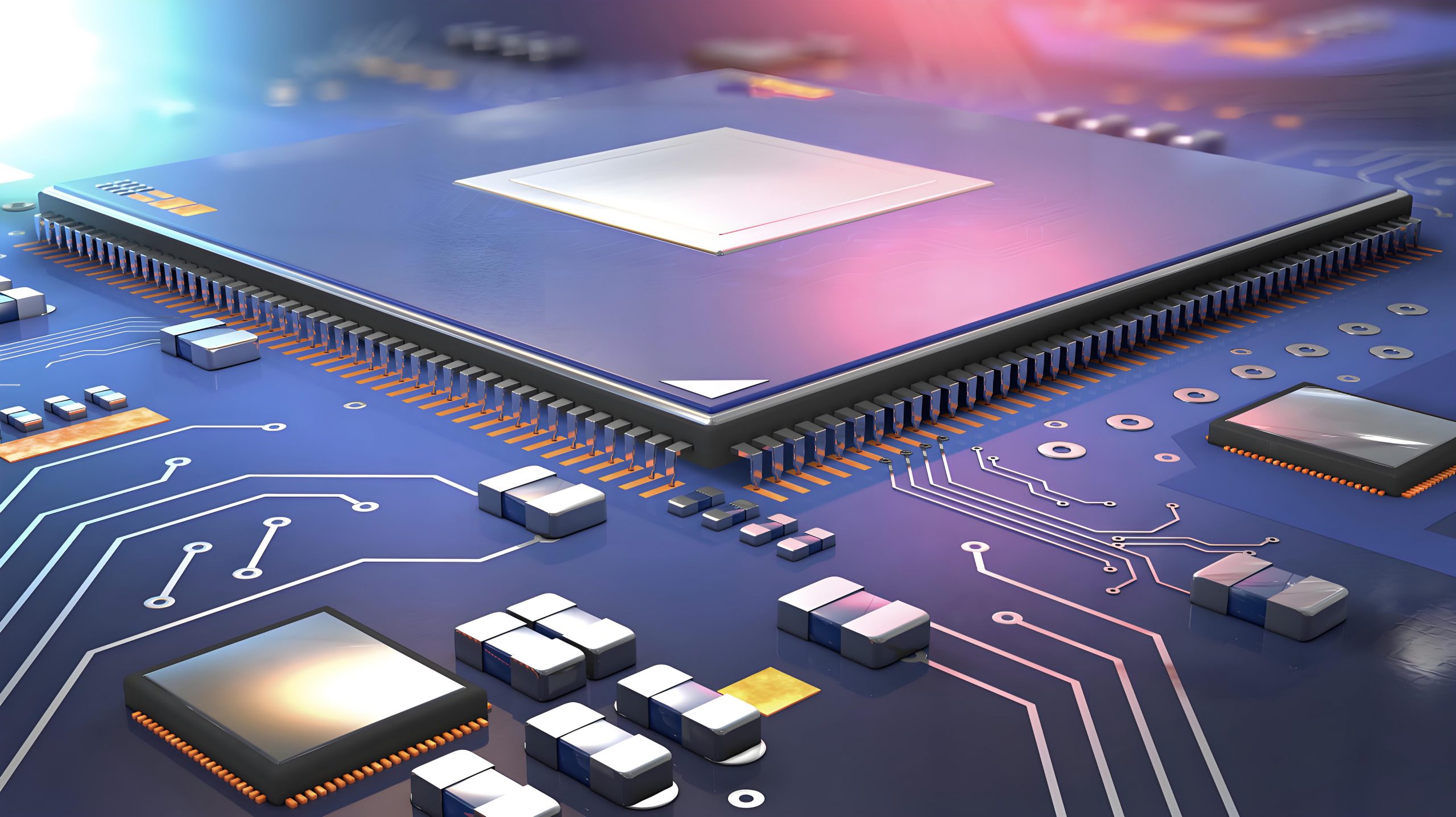